Forte de près de 50 ans d’expérience, l’usine de valorisation thermique des résidus de Wesseling est spécialisée dans l’élimination professionnelle et fiable des déchets spéciaux. Pour assurer son bon fonctionnement, l’incinérateur à haute température fait l’objet d’une révision annuelle approfondie qui s’étend sur plusieurs semaines. En 2024, ces opérations de maintenance ont pris une tournure historique : en plus des travaux d’entretien réguliers, des mesures d’assainissement majeures ont été mises en œuvre, dans le but d’augmenter l’efficacité mais également d’améliorer significativement la fiabilité de l’installation. Une rétrospective de cette révision historique…
La société TRV à Wesseling
La société TRV, Thermische Rückstandsverwertung GmbH & Co. KG, est une entreprise du groupe REMONDIS Industrie Service. Exploitée depuis 1974, l’usine d’incinération de déchets spéciaux située dans la zone industrielle de Wesseling est spécialisée dans l’élimination professionnelle des déchets dangereux. Il s’agit de valoriser ou d’éliminer ces derniers dans le respect de l’environnement et des règlementations en vigueur. Qu’ils soient solides, pâteux, liquides ou conditionnés en emballages, les déchets font l’objet d’un traitement thermique.
Les capacités de réception et de traitement dans la trémie pour déchets solides sont de l’ordre de 800 m3 tandis que les conteneurs pour déchets liquides peuvent accueillir environ 950 m3.
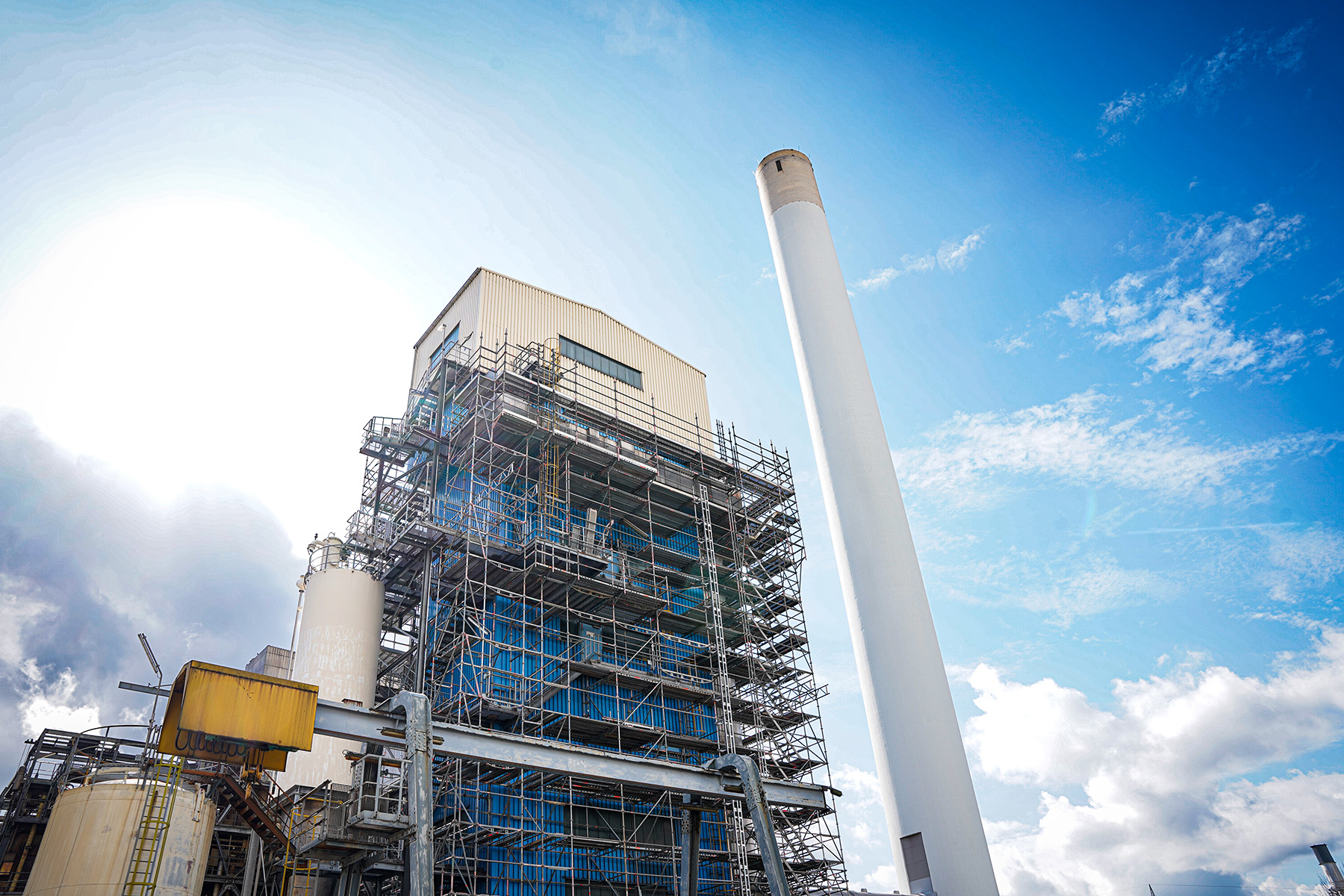
Mode de fonctionnement et structure
La TRV est la seule usine d’incinération de déchets spéciaux en Allemagne capable de traiter thermiquement tous les types de déchets, quel que soit leur code. Elle constitue donc un élément incontournable du réseau d’installations de REMONDIS Industrie Service. Composée de deux lignes de traitement, l’installation utilise deux fours rotatifs dans lesquels les déchets spéciaux sont traités thermiquement à une température pouvant atteindre 1.100 degrés Celsius. Les lignes de traitement comprennent, en aval des fours rotatifs, deux chambres de postcombustion situées directement derrière les fours, deux chaudières de récupération dans lesquelles de la vapeur est produite à partir de l’énergie dégagée par les gaz de combustion chauds. Plusieurs étapes d’épuration permettent ensuite d’éliminer les substances nocives qui subsistent dans ces gaz de combustion et de réduire les émissions à un minimum.
Une maintenance annuelle pour garantir le bon fonctionnement
Une fois par an, le site est à l’arrêt total et une révision de plusieurs semaines est effectuée afin d’assurer la pérennité de la capacité de traitement de l’installation. Ce principe ne s’applique pas uniquement à la société TRV de Wesseling, mais à toutes les installations du réseau REMONDIS Industrie Service. Pendant cette période d’arrêt programmée, des travaux de construction et de maintenance nécessaires sont réalisés en collaboration avec différents corps de métier, ce qui ne serait pas possible si l’installation fonctionnait normalement. Chez TRV, un volet essentiel de la révision annuelle consiste notamment à rénover les fours tubulaires rotatifs, qui sont maçonnés de l’intérieur avec un matériau spécial résistant à la chaleur. Une fois les fours tubulaires rotatifs refroidis, des travaux de maçonnerie et de réparation sont effectués au sein des tubes rotatifs. Tous les composants de l’installation sont nettoyés, les pièces usagées sont remplacées et les réparations nécessaires effectuées. Ces travaux de révision sont également l’occasion d’éliminer les risques de défaillance. C’est pourquoi ils constituent une phase essentielle pour le bon fonctionnement de l’exploitation pendant le reste de l’année car ils permettent d’éviter les pannes et les dysfonctionnements.
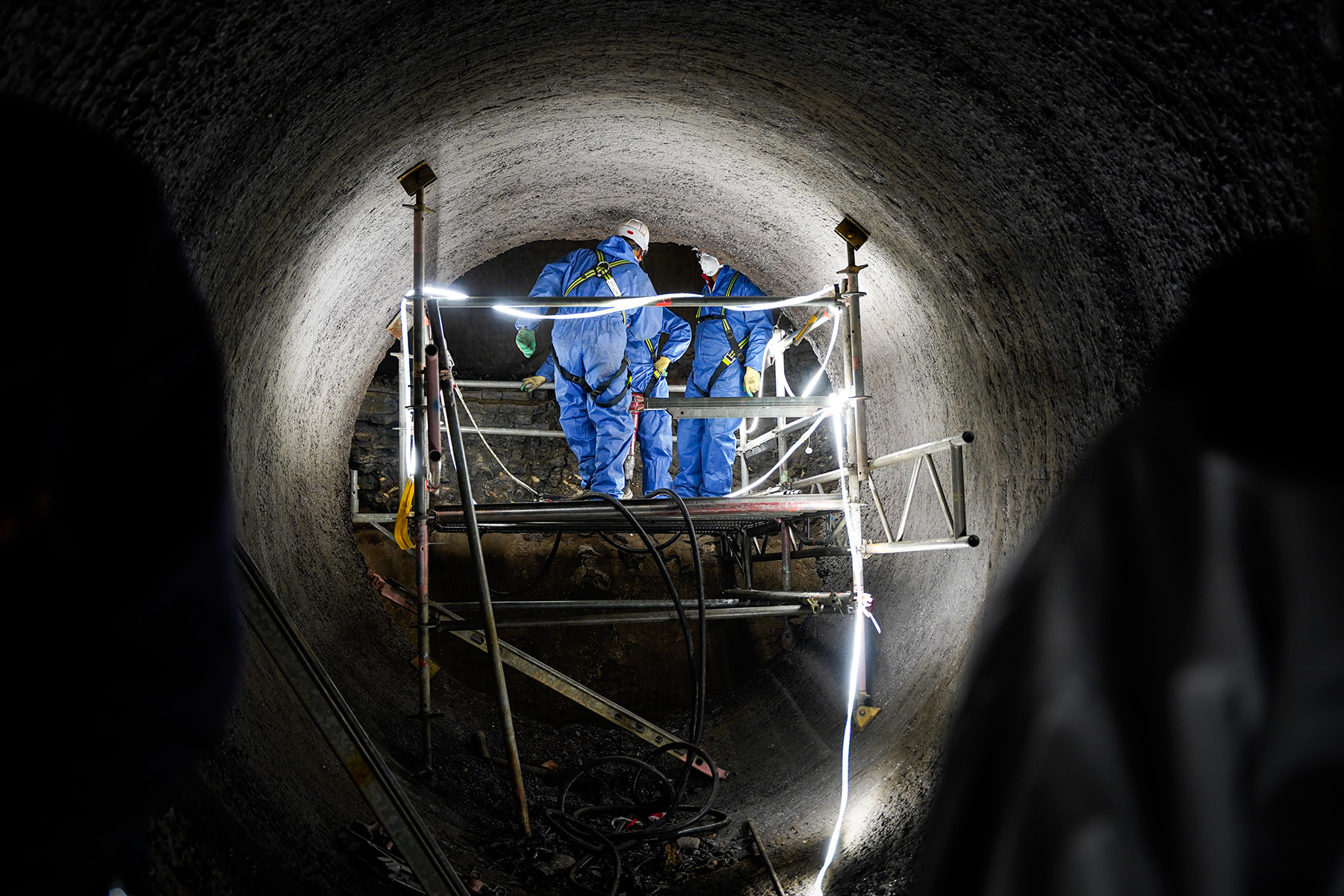
Une rénovation d’une ampleur exceptionnelle
Alors en quoi cette révision-là a-t-elle été si exceptionnelle ? Et plus particulièrement la rénovation des deux chaudières de récupération et de l’adsorbeur de flux d’air. Les deux chaudières de récupération produisent de la vapeur grâce aux gaz de combustion chauds issus de la valorisation thermique des déchets spéciaux dans les tubes rotatifs. Celle-ci est ensuite réinjectée sous forme de source d’énergie dans le réseau du site. Les chaudières constituaient le point névralgique des rénovations. Il s’agissait d’augmenter le taux de fiabilité et de disponibilité de l’installation et d’éviter les défaillances. Les chaudières étant limitées thermiquement, la réhabilitation n’a toutefois pas entraîné d’augmentation de la puissance.
L’adsorbeur à courant d’air marque la dernière étape de nettoyage dans le processus d’épuration des gaz de combustion et élimine les polluants restants grâce à un total de 660 manchons filtrants. L’assainissement de cette partie de l’installation a eu un impact considérable, nettement perceptible après la révision. Pour traiter les déchets dans un tube rotatif, il faut de l’oxygène. C’est pourquoi on introduit de l’air dans le tube rotatif. Celui-ci est aspiré dans toute l’installation et à toutes les étapes du traitement grâce à la dépression qui y règne et à plusieurs ventilateurs intégrés. Avant la rénovation, de l’air provenant de l’extérieur était aspiré, en même temps que l’air ambiant, au niveau de l’adsorbeur de flux d’air. La révision a permis de supprimer ce phénomène. Le flux d’air peut donc désormais circuler plus efficacement dans l’installation, réduisant ainsi considérablement la consommation énergétique.
Cette phase de remise en état a mobilisé 24 heures sur 24 quelque 500 collaborateurs venus de 36 entreprises partenaires, soit environ deux fois plus que lors d’une révision annuelle normale. Effectuées conjointement aux travaux de maintenance habituels, ces mesures visent à améliorer l’efficacité et la disponibilité de l’installation.
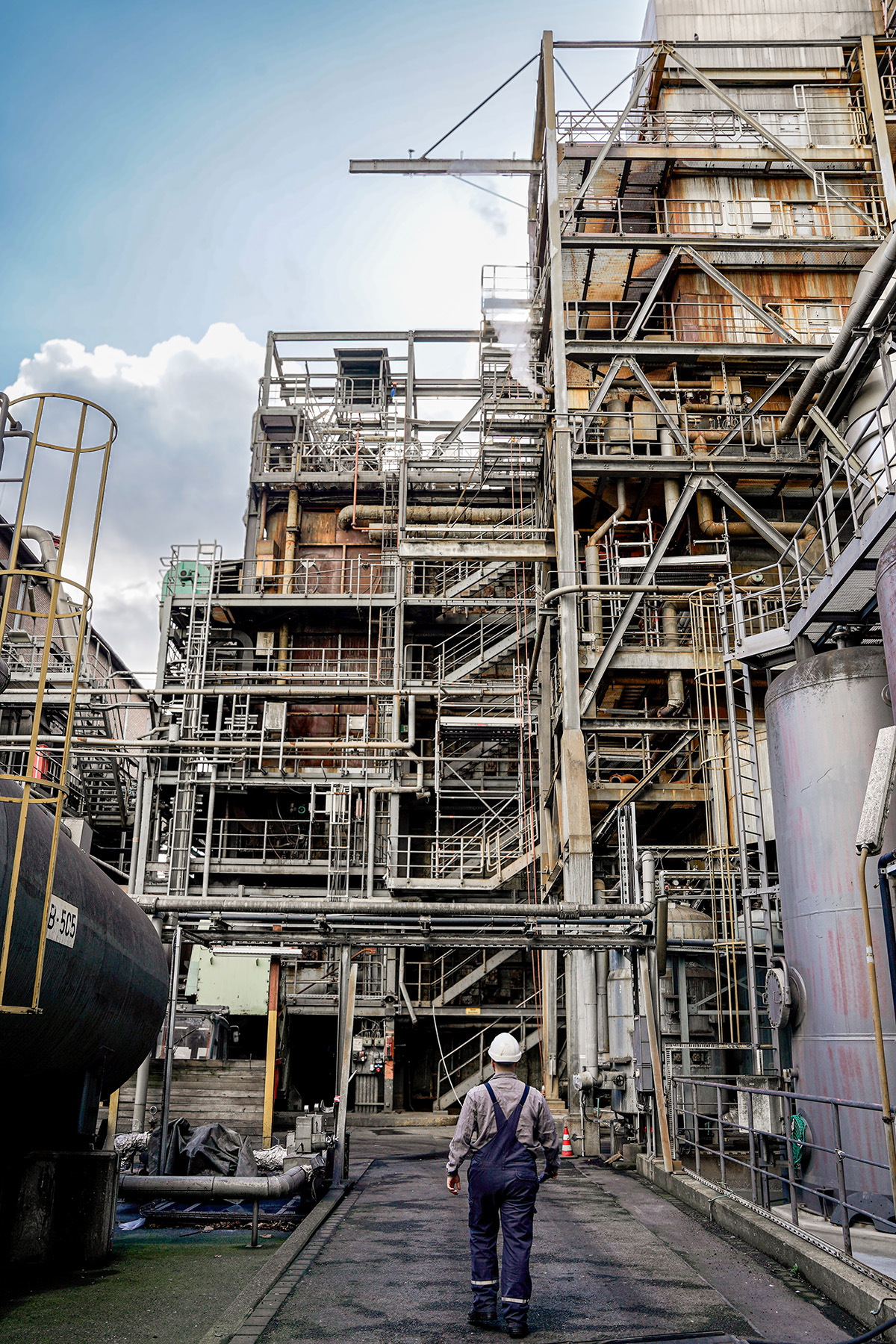
Les effets de la révision sur le fonctionnement de l’installation
Conséquence de la rénovation : les conditions de fonctionnement de l’installation sont désormais bien différentes. Les quantités d’air peuvent être adaptées aux conditions de combustion de manière plus souple, l’efficacité a été améliorée et les dépenses énergétiques réduites. Mais surtout, les différentes mesures prises lors de la rénovation ont permis de rendre le fonctionnement de l’installation plus fiable et plus constant.
« Grâce aux travaux, l’objectif que nous nous étions fixé a été atteint : les mesures mises en œuvre diminuent les cas de panne et concourent à une meilleure disponibilité de l’installation, augmentant considérablement sa fiabilité… »
Kai Reinicke, Directeur de la société TRV
Des défis de taille
Sur un projet de cette envergure, une planification minutieuse et une coordination efficace sont primordiales. Contrairement aux opérations de maintenance annuelles, où la plupart des processus sont bien rodés au fil des ans, de nouveaux facteurs étaient à prendre en compte cette année. Avec une équipe de planification composée à la fois de collaborateurs de la maintenance et de l’exploitation, la préparation a commencé bien en amont. L’enjeu était notamment de coordonner le calendrier entre les différents corps de métier impliqués et les nombreuses livraisons. Bien souvent, chaque minute comptait – au sens propre du terme.
René Kolz, directeur de la maintenance, et Jens Schmitz, directeur des opérations chez TRV, résument :
« Dix-neuf mois se sont écoulés entre le début de la planification et la mise en œuvre du projet. Dès le début, nous avons travaillé d’arrache-pied pour que ce projet soit parfaitement ficelé. Avec autant d’interdépendances entre les différents corps de métier, nous ne pouvions pas nous permettre le moindre faux pas. Comme souvent, la météo a été un facteur d’incertitude. Mais malgré de nombreux jours de pluie, nous avons eu de la chance. Lors des principales opérations de grutage, notamment, le temps a toujours été stable ».
Grâce à une équipe très investie, la révision s’est déroulée sans accroc et l’excellente préparation et la coordination entre les intervenants ont permis d’achever les opérations les délais prévus. Nous remercions tout particulièrement les nombreux partenaires qui ont largement contribué à la réussite de cette opération !
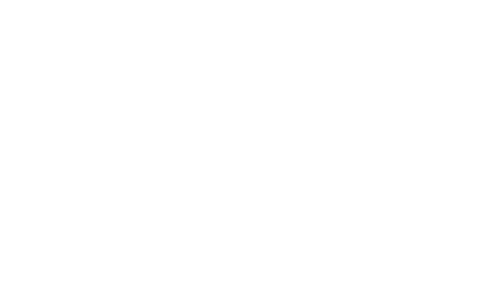
Crédits photographiques : © REMONDIS